Introduction:
In the realm of piping systems, branch connections play a crucial role in ensuring the smooth and efficient flow of fluids. Olet fittings have emerged as a preferred choice for creating branch connections, offering various advantages over conventional methods. In this comprehensive guide, we will delve into the different aspects of Olet fittings, from their types and installation procedures to the materials of construction and the codes and standards governing their usage.
Branch Connection Types:
Olet fittings are a family of branch connection fittings that come in various types to suit different requirements. The primary types of Olet fittings include Weldolet, Sockolet, Threadolet, Elbolet, and Nipolet. Each type serves a specific purpose and is selected based on factors such as pipe size, pressure, and temperature conditions.
Why Prefer Olets Fittings Over Conventional Branch Connection?
- Reduced Welding and Fabrication Time:Olet fittings significantly reduce welding and fabrication time compared to traditional branch connections. Their pre-shaped design eliminates the need for intricate welding processes, saving both time and labor costs.
- Minimized Stress Concentration:Olets distribute stress more uniformly across the piping system, reducing the risk of stress concentration points. This design feature enhances the overall integrity and longevity of the pipeline.
- Cost-Effectiveness:The efficiency and ease of installation of Olet fittings contribute to cost-effectiveness. The reduction in labor hours, coupled with the minimized need for specialized skills, makes Olet fittings an economically sound choice.
Olets Fitting Types:
- Weldolet:Weldolet is the most common type of Olet fitting. It is welded onto the main pipe and provides a sturdy branch connection.
- End: Bevel end
- Branch Pipe End: Bevel end
- Size Range: 2″ – 24″
- Commonly Used Size Range: 2″ – 8″
- Thickness/Schedule: Same as the pipe
- Sockolet:Sockolet is suitable for low-pressure applications and is socket-welded onto the pipe. It is commonly used in smaller pipe sizes.
- End: Socket type
- Branch Pipe End: Plain end
- Size Range: 1/2″ – 4″
- Commonly Used Size Range: 1/2″ – 2″
- Thickness/Schedule: 3000#, 6000#, and 9000# (ratings for socket weld fittings)
- Threadolet:Threadolet is threaded onto the pipe, making it suitable for applications where welding is not preferred or feasible.
- End: Female Threaded
- Branch Pipe End: Male threaded
- Size Range: 1/2″ – 2″
- Thickness/Schedule: 2000#, 3000#, and 6000# (ratings for threaded fittings)
- Elbolet:Elbolet is designed for 90-degree branch connections, offering versatility in various piping configurations.
- End: Female Threaded, Socket Weld, and Bevel end
- Branch Pipe or Instrument End: Male Threaded, Plain, and Bevel end
- Size Range: 1/2″ – 2″ NPS (for threaded and socket weld end), Above 2″ NPS (for threaded and socket weld end)
- Thickness/Schedule: 3000# and 6000# (for socket and threaded end), Rating for Buttweld end – same as piping system
- Nipolet:Nipolet is a combination of Weldolet and Threadolet, allowing for both welding and threading options in a single fitting.
- End: Female threaded or Socket weld end
- Branch Component End: Male threaded or Plain end
- Size Range: 1/2″ – 2″ (preferred size range)
- Rating: 3000# and 6000#
- Sweepolet:Sweepolet is typically used when the header size is above 24″ NPS, and the branch size is above 8″ NPS. Its primary functions include reducing pressure drop and facilitating the free-draining of fluid.
- Where to Use: Typically employed if the header is above 24″ NPS, and the branch is above 8″ NPS; used for reducing pressure drop and free-draining of fluid; utilized in radiography requirements.
- End: Bevel end
- Branch Pipe End: Bevel end
- Size Range: 8″ – 24″
- Thickness/Schedule: Same as the pipe/Schedule Number
- Latrolet:Latrolet is a versatile fitting designed for various applications. It offers flexibility with threaded, socket weld, and beveled end options. It is often used in radiography-required situations and can be employed below 2″ NPS for certain fluid applications.
- End: Female Threaded, Socket Weld, and Bevel end
- Branch Pipe End: Male Threaded, Plain, and Bevel end
- Size Range: 1/2″ – 2″ NPS (for threaded and socket weld end), Above 2″ NPS (for threaded and socket weld end)
- Thickness/Schedule: 3000# and 6000# (for socket and threaded end), for Bevel end thickness will be the same as pipe or system rating; Bevel/butt weld fittings can be used below 2″ NPS (for food, pharma, and corrosive fluid)
- Flangolet:Flangolet stands out with its flanged ends, providing a connection method compatible with ASME B16.5 flange end preparation. It is commonly used across various industries and applications.
- End: Flanged end
- Branch Component End: Flanged end
- Size Range: 1/2″ – 24″ (Normally available)
- Rating: 150#, 300#, 600#, 900#, 1500#
- Flange End Preparation: ASME B16.5
- Coupolet:Coupolet is a specialized fitting designed for applications where a female threaded end is needed on the main pipe and a male threaded end is required on the branch or fire sprinkler system. It provides a secure and reliable connection.
- End: Female threaded end
- Branch Component or Fire Sprinkler End: Male threaded end
- Size Range: 1/2″ – 2″ (preferred size range)
- Rating: Can be used up to a maximum of 300#
- Thickness/Schedule: 2000#, 3000#, and 6000#
- Inserted Weldolet:Inserted Weldolet is commonly used when the piping system is less critical. It offers ease of installation and is cost-effective for applications where criticality is not a primary concern.
- End: Bevel end
- Branch Pipe End: Bevel end
- Size Range: 8″ – 24″ (mostly used size range), but the piping system should be less critical
- Thickness/Schedule: Same as the pipe/Schedule Number
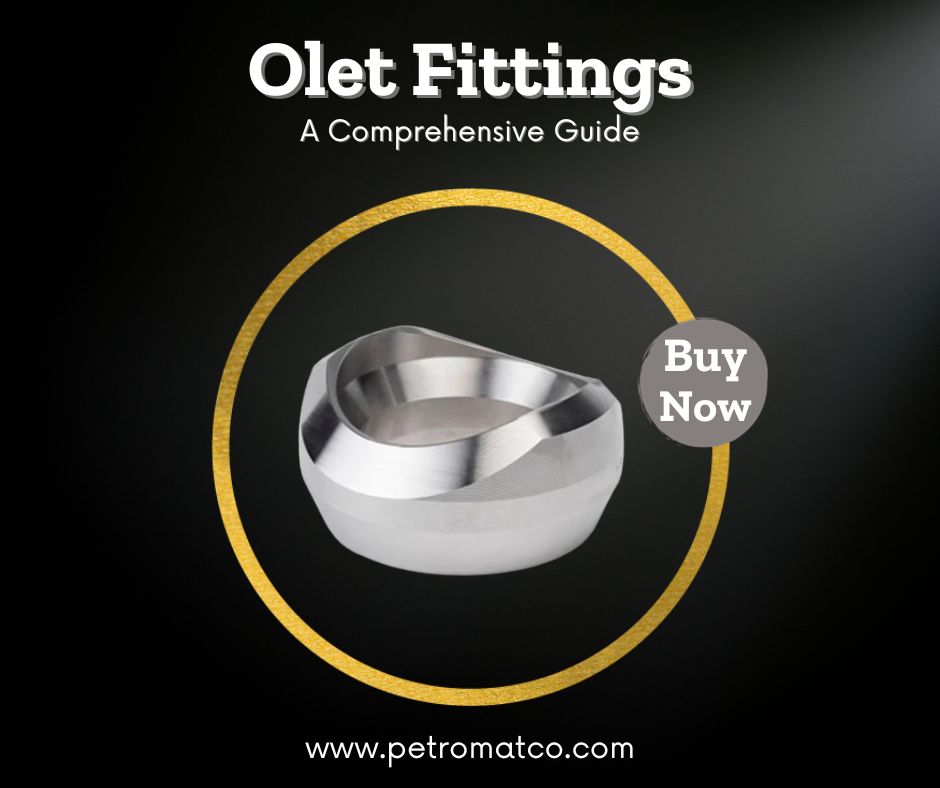
exploring-olet-fittings-a-comprehensive-guide
Weldolet Installation Procedure:
- Preparation:Ensure the main pipe is clean and free from contaminants. Cut an appropriate hole for the Olet fitting, considering the specific type being used.
- Fitment:Align the Olet fitting with the hole and tack weld it into place. Verify the alignment and dimensions before proceeding with the final welding.
- Welding:Complete the welding process according to the welding procedure specifications. Ensure the weld is of high quality, free from defects, and meets the required standards.
Data Required for Ordering Branch Fittings:
- Pipe Size and Schedule:Specify the size and schedule of the main pipe to ensure proper fitting selection.
- Type of Olet Fitting:Clearly indicate the type of Olet fitting required for the specific application.
- Material Grade:Specify the material grade for both the main pipe and the Olet fitting to ensure compatibility and corrosion resistance.
- Pressure and Temperature Ratings:Provide the expected pressure and temperature conditions to select Olet fittings that meet the required ratings.
Materials of Construction:
Olet fittings are available in a wide range of materials to suit diverse applications. Common materials include carbon steel, stainless steel, alloy steel, and other special alloys. The material selection is crucial to ensure compatibility with the fluid being transported and to resist corrosion in the operating environment.
Selecting the right material for Olet fittings is vital for performance and longevity. Common materials include:
- A105 – For Carbon Steel (CS) Olets Fittings
- A350 Gr. LF2 – For Low-Temperature Carbon Steel (LTCS) Olets Fittings
- A182 Gr. F11, A182 Gr. F22, A182 Gr. F5, A182 Gr. F9, A182 Gr. F91, A182 Gr. F92 – For Low Alloy Steel (LAS)
- A182 Gr. F304, A182 Gr. F316, A182 Gr. F321, A182 Gr. F347 – Stainless Steel (SS)
Codes and Standards:
The manufacturing and installation of Olet fittings are governed by industry standards and codes to ensure safety and reliability. Some commonly referenced standards include ASME B16.9, ASME B31.3, and MSS SP-97. Adhering to these standards is essential for compliance with regulatory requirements and ensuring the longevity of the piping system.
- MSS-SP-97 – Manufactured Standard Society – Special Practices – Used for Dimensioning
- ASME B16.9 – For Buttweld Fittings
- ASME B16.11 – For Threaded and Socket weld Fittings
- ASME B16.25 – For Buttweld/Bevel End Preparation
- ASME B1.20.1 – For Thread End Preparation
- ASME B16.5 – For Flanged End Fittings
Conclusion:
Olet fittings have revolutionized the way branch connections are made in piping systems, offering efficiency, cost-effectiveness, and enhanced structural integrity. Understanding the various types, installation procedures, material considerations, and compliance with industry standards is essential for making informed decisions in selecting and using Olet fittings. As the demand for efficient and reliable piping solutions continues to grow, Olet fittings stand out as a reliable choice for creating robust branch connections in diverse applications.
Outlet Pipe Fittings – Petromatco.com by petromatcompany on Scribd